Comparing Welding Techniques: When to Choose Electro Fusion vs. Butt Fusion
In the world of pipeline welding, selecting the right technique is essential to ensuring durable, leak-free connections. Whether you’re working on a small-scale repair or a large infrastructure project, choosing between electro fusion and butt fusion welding can significantly impact the performance and longevity of your pipework.
At Pipe Testing Services (PTS), we specialise in both techniques and offer expert advice to help you choose the best method for your needs. This guide explores the core differences between electro fusion and butt fusion welding, providing a detailed comparison to help you make an informed decision for your project
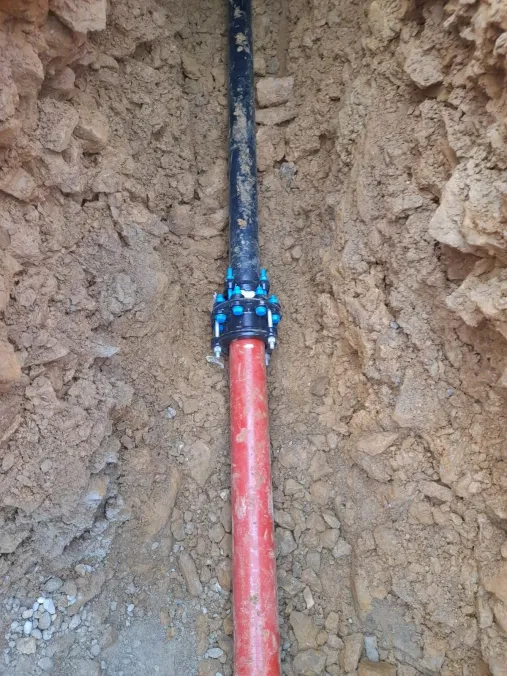
Understanding Electro Fusion and Butt Fusion Welding
Electro Fusion Welding: A Closer Look
Electro fusion welding uses electrical resistance to heat and fuse the pipes at the joint. This process involves the insertion of a fitting with built-in electric heating coils, which heat the pipe surfaces until they melt and fuse together. The controlled heating ensures a precise and durable joint.
Advantages of Electro Fusion
- Versatility: Ideal for joining pipes of varying diameters, including smaller sizes (16mm-630mm), and can accommodate irregular joint configurations.
- Space Efficiency: Perfect for tight spaces, as the equipment is compact and portable, making it the go-to option for confined or hard-to-reach areas.
- Reliability: Frequently used for pipeline repairs due to its ability to form secure connections on existing infrastructure.
- Minimal Preparation: The electro fusion process requires minimal surface preparation compared to other methods, reducing the time needed for set-up.
Butt Fusion Welding: A Closer Look
Butt fusion welding, also known as butt-welding, involves heating the ends of two pipe segments until they become molten, then pressing them together to form a seamless joint. This method creates a strong, homogeneous bond between the two pipes, making it a preferred choice for large-scale, long-term pipeline installations.
Advantages of Butt Fusion:
- High Strength Joints: The resulting joints are exceptionally strong, capable of handling high pressure and demanding operational conditions.
- Cost-Effectiveness for Large Projects: Ideal for joining large-diameter pipes (50mm-2m), especially in projects where the joint strength and material integrity are critical.
- Efficiency: Butt fusion welding allows for high-speed, bulk welding, making it ideal for large-scale infrastructure projects like water distribution networks, gas pipelines, and industrial systems.
- Durability: Creates long-lasting, seamless joints that maintain their integrity over time.
When to Choose Electro Fusion vs. Butt Fusion: Key Factors to Consider
The decision to use electro fusion or butt fusion welding depends on several factors, each of which should be evaluated carefully. At PTS, our expertise allows us to help you make the best choice for pipe fusion welding services that best suit your project’s specific needs.
Pipe Size and Project Scope
Small to Medium Pipes (16mm-630mm): Electro fusion is the better option due to its flexibility and suitability for varied pipe diameters and configurations.
Large Pipes (50mm-2m): Butt fusion is more cost-effective and efficient for larger pipes, as it allows for faster processing of high volumes and thicker materials.
Location and Accessibility
Confined Spaces: Electro fusion is ideal for hard-to-reach areas due to its compact nature and ease of use in confined spaces.
Open and Large-Scale Projects: Butt fusion is better suited for large, open environments where larger equipment can be utilized, and long, straight runs are required.
Joint Complexity and Precision
Complex Joints and Tight Tolerances: Electro fusion allows for highly precise joints in complex configurations, making it the best choice for intricate pipework.
Simple, Straight Joints: Butt fusion is faster and more economical for joining pipes in straight runs, where precision is less of a concern.
Environmental Conditions
Adverse Weather: Electro fusion welding is less affected by environmental factors such as extreme temperatures, rain, or high winds, making it ideal for outdoor or challenging weather conditions.
Controlled Environments: Both methods perform well in a controlled environment, but butt fusion requires optimal conditions for heating and pressure control.
Project Timeline and Efficiency
Fast Turnaround: Butt fusion welding is typically faster for larger projects, as the process can handle high volumes of work quickly.
Precision and Quality: Electro fusion ensures high precision, particularly in smaller or more intricate applications.
PTS's Expertise: Comprehensive Solutions for Your Welding Needs
At PTS, we pride ourselves on offering expert welding services for both electro fusion and butt fusion methods. With years of industry experience and certified technicians, we provide tailored solutions designed to meet the unique demands of your project.
Why Choose PTS for Your Welding Needs?
- Certified Technicians: Our team is fully trained and experienced in both electro fusion and butt fusion techniques, ensuring top-quality welds and adherence to industry standards.
- State-of-the-Art Equipment: We use the latest welding technologies and tools to deliver precise, durable joints that meet your project specifications.
- Tailored Solutions: No two projects are the same. We work with you to assess the specific needs of your project and recommend the most efficient welding technique.
- Commitment to Quality: We ensure all joints meet regulatory and quality standards, providing long-lasting solutions for water utilities, construction, and manufacturing projects.
Industry-Specific Applications
Water Utilities: Ensuring leak-free, durable pipeline connections is critical in water infrastructure. We specialize in providing reliable welding services that meet stringent industry standards, safeguarding water quality.
Construction Projects: Whether you’re working on new construction or pipeline upgrades, our expert welding services ensure timely project delivery while maintaining budgetary constraints.
Manufacturing Pipelines: For industries where pipeline integrity is paramount to operations, PTS offers precise welding solutions that keep your processes running smoothly and without interruption.
Considerations for Choosing the Right Welding Method
Long-Term Cost Considerations
Initial Investment: Electro fusion equipment typically comes with higher upfront costs due to the complexity of the machinery, but offers greater versatility. Butt fusion, however, has lower consumable costs, making it more budget-friendly for large-scale projects.
Environmental Impact
- Electro Fusion: Better suited for challenging environmental conditions, such as extreme temperatures, moisture, or dusty environments.
- Butt Fusion: Requires optimal environmental control to ensure uniformity and consistency during the welding process.
Operator Expertise and Training
Both welding methods require skilled operators to ensure proper alignment, cleaning, and fusion settings. PTS provides ongoing training to our team to maintain the highest standards of quality and efficiency.
Contact PTS for Tailored Welding Solutions
At Pipe Testing Services, we understand the importance of selecting the right welding method for your project. Whether you require electro fusion or butt fusion welding, our team is ready to assist you with expert advice and top-quality services.
- Phone: 01922 451646
- Email: enquiries@pipetestingservices.co.uk
- Address: Unit 27 Birchbrook Industrial Estate, Shenstone, Lichfield, Staffs, WS14 0DJ
Contact us now to schedule a consultation or to receive a personalised quote for your next project. Let us help you ensure the safety, reliability, and durability of your pipeline systems.
FAQs: Your Questions Answered – Pipe Welding Techniques
What is the main difference between electro fusion and butt fusion?
Electro fusion uses electrical resistance to join pipes, whereas butt fusion involves heating and pressing pipe ends together to create a seamless joint.
Which method is more cost-effective?
Butt fusion is typically more cost-effective for large-scale projects, while electro fusion is preferred for smaller-scale or more intricate applications.
Can electro fusion and butt fusion be used together?
Yes, these techniques are often used in combination, particularly in projects with varying pipe sizes and configurations.
Which industries use these methods?
Both methods are widely used in water utilities, construction, and manufacturing industries for reliable, long-lasting pipeline connections.
How do environmental conditions affect welding?
Electro fusion is more resistant to environmental factors like extreme weather, while butt fusion requires controlled conditions for optimal results.
Is operator skill important for both methods?
Yes, skilled technicians are crucial for ensuring precise fusion settings and proper alignment for both welding methods.