Pneumatic Leak Testing Services UK
Verifying the integrity of newly installed, repaired, or modified pipelines and pressure systems is crucial before they enter service. Pneumatic leak testing offers a highly effective and often advantageous method for detecting leaks using compressed air or inert gas. Pipe Testing Services (PTS) provides expert pneumatic leak testing services across the UK for various applications, particularly within water infrastructure and related industries.
What is Pneumatic Leak Testing?
Pneumatic leak testing involves pressurising an isolated section of pipework or a vessel with compressed air or an inert gas (like nitrogen) to a specified test pressure. Sensitive gauges and detection equipment are then used to monitor for pressure drops, which indicate leaks. This method is valued for its cost-effectiveness, safety in many scenarios (avoiding water use), and the relative ease with which escaping gas can sometimes be detected compared to water. Early leak identification prevents potential product loss, environmental issues, and ensures the reliability of subsequent commissioning steps like hydrostatic pressure testing.
In need of services – take a look here. Alternatively, take a look at our dedicated site for Hydrostatic pressure testing
How PTS Performs
Pneumatic Leak Testing
Our process utilizes compressed air or inert gas to safely pressurise the system under evaluation.
The isolated section of the pipeline or vessel is carefully filled with the chosen gas. Pressure is gradually increased to the required test level, meticulously monitored using calibrated gauges. Throughout the test duration, our technicians use sensitive equipment and proven techniques (like applying leak detection solutions or using ultrasonic detectors) to identify any pressure drops or pinpoint the exact location of leaks.
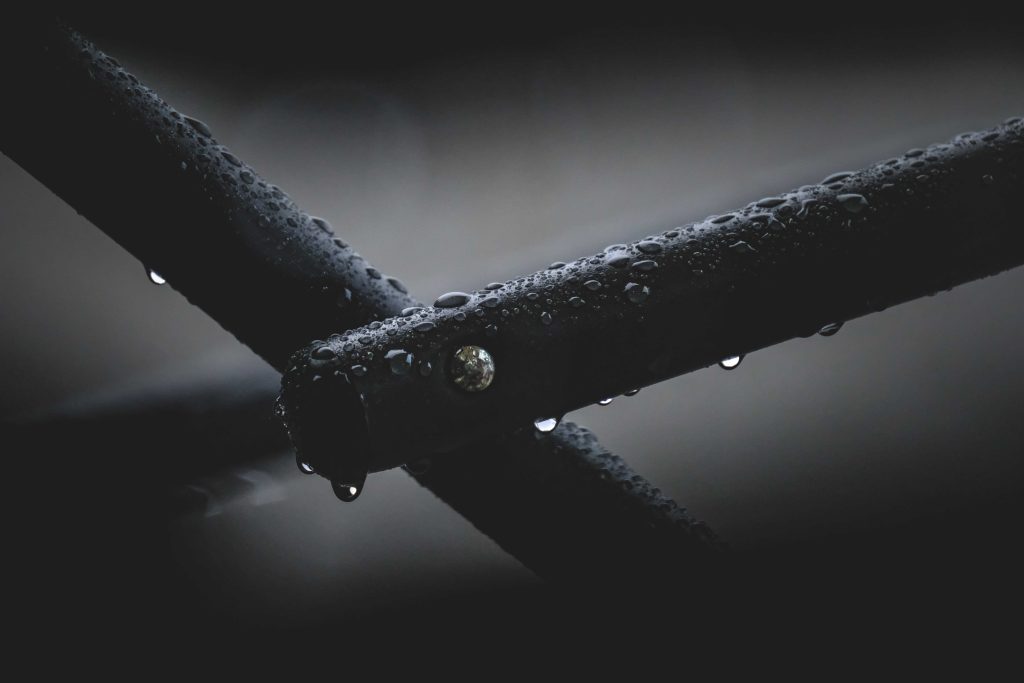
When is Pneumatic
Leak Testing Recommended?
PTS regularly employs pneumatic leak testing in several key scenarios:
- New Pipeline Installations: To identify leaks or defects introduced during construction before filling with water or product, saving time and resources.
- Testing Gas Lines: It's the standard method for testing pipelines intended for gas transmission or distribution.
- Systems Where Water is Undesirable: Ideal for systems where introducing water for hydrostatic testing could cause contamination, corrosion, or operational issues.
- Repaired or Modified Sections: Verifying the integrity of welds, joints, or repairs before returning a system to service.
- Pre-commissioning Checks: As a crucial step in ensuring vessel or tank integrity prior to full hydrostatic testing or operational use.
The PTS Pneumatic
Leak Testing Procedure
Our standard procedure, adaptable to specific site requirements, typically involves:
System Preparation & Isolation
The specific section to be tested is safely isolated using appropriate end closures, valves, or blanks. Temporary connections for gas introduction, pressure monitoring, and safety relief systems are securely installed.
Pressurisation
The isolated section is slowly filled with compressed air or the specified inert gas. Pressure is gradually increased in stages to the agreed test pressure, adhering strictly to project specifications and safety limits.
Leak Detection & Monitoring
Once at pressure, the system is monitored for a defined period using calibrated pressure gauges and data loggers. Technicians actively search for leaks using appropriate methods (e.g., soapy water solutions, ultrasonic detectors) at joints, flanges, and other potential weak points.
Depressurisation & Reporting
Upon successful completion (or after identifying leaks), the system is safely depressurised following established protocols. Any identified leaks are documented for repair. PTS provides a comprehensive report detailing the test parameters, procedure, results, and any findings.
Limitations and Relationship
to Hydrostatic Testing
While highly effective, pneumatic testing has considerations. The stored energy in compressed gas requires stringent safety protocols during testing. It may not always detect defects that only manifest under the different stress conditions imposed by hydrostatic (water) pressure.
For many applications, particularly pressure vessels and pipelines designed for liquids, pneumatic leak testing serves as an invaluable preliminary check to identify gross leaks before proceeding to a full hydrostatic pressure test, which remains the definitive method for verifying structural integrity under liquid pressure for many systems. PTS can advise on the most appropriate testing regime for your specific needs, often employing both methods where required.
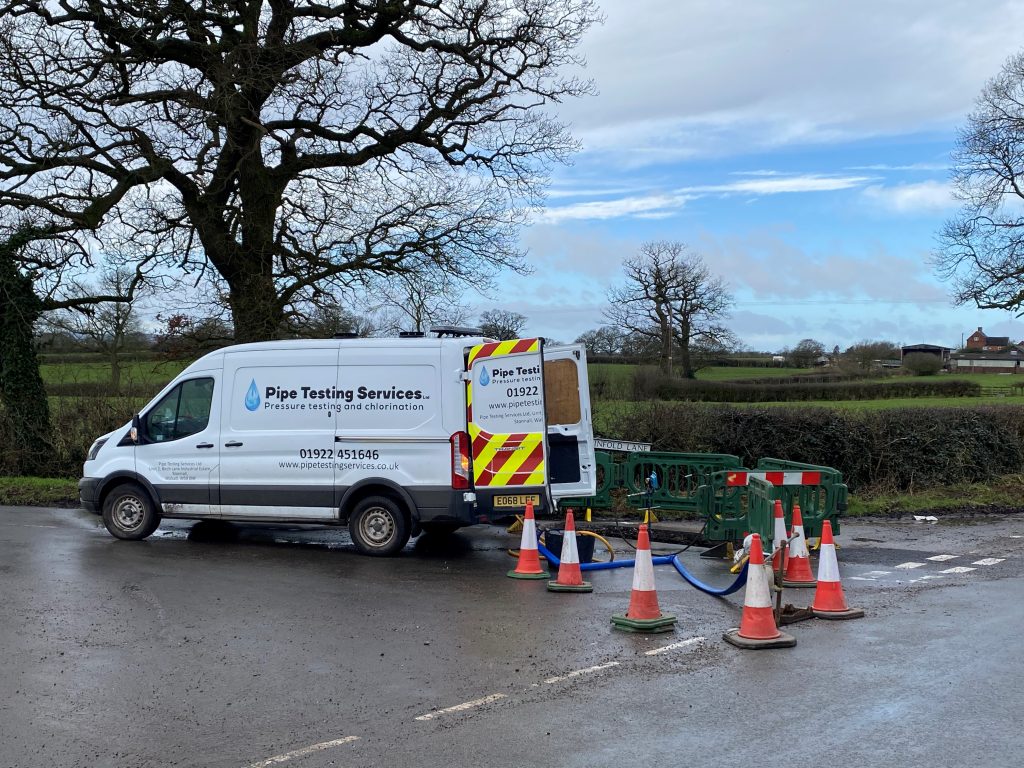
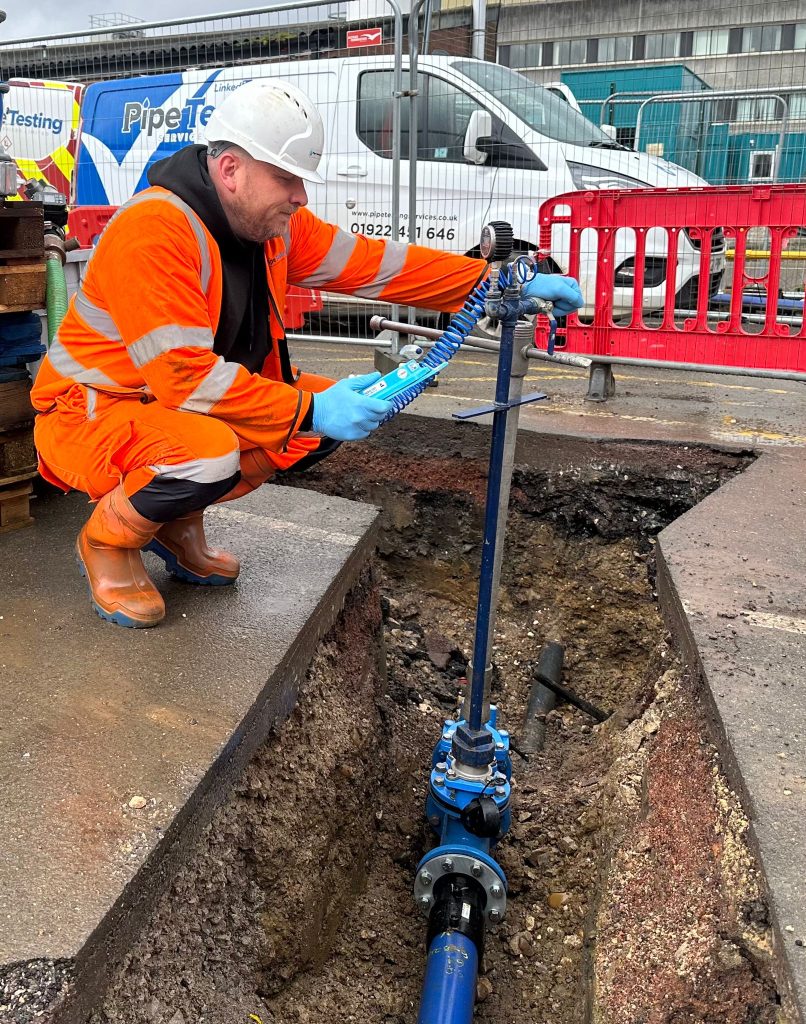
Why Choose PTS for Pneumatic Leak Testing?
Selecting PTS for your pneumatic testing needs ensures:
- Experienced & Certified Technicians: Our team is highly trained and experienced in conducting pneumatic tests safely and effectively across various pipeline and vessel types.
- Specialised Equipment: We utilise calibrated, high-quality pressure gauges, data loggers, safety relief systems, and leak detection equipment.
- Strict Safety Protocols: Safety is paramount. We adhere rigorously to industry best practices and established safety procedures for pressurised gas testing.
- Nationwide UK Coverage: We provide reliable pneumatic testing services across England, Scotland, Wales.
- Clear & Compliant Reporting: You receive detailed test certificates and reports suitable for commissioning packages and regulatory requirements.
- Integrated Services: PTS offers a full suite of testing services, allowing for seamless transition between pneumatic and hydrostatic testing or other commissioning activities like pipeline flushing and chlorination.
Contact PTS for Expert
Pneumatic Leak Testing
Ensure the integrity and safety of your pipelines and pressure systems with professional pneumatic leak testing from PTS. To discuss your project requirements, schedule testing, or request a quote for pneumatic leak testing services, please contact our expert team:
Phone – 01922 451646
Email – enquiries@pipetestingservices.co.uk
Address – Unit 27 Birchbrook Industrial Estate, Shenstone, Lichfield, Staffs, WS14 0DJ
Partner with PTS for reliable, safe, and comprehensively documented pressure testing solutions across the UK.