Expert Pipe Fusion Welding Services for PE Pipe Systems
Pipe Testing Services provides expert pipe fusion welding services across the UK, offering a reliable and robust method for creating strong, permanently leak-proof joints in polyethylene (PE) pipe systems. Our certified technicians specialise in the two primary techniques: butt fusion and electrofusion. We work on pipe sizes from 20mm up to 630mm, ensuring quality and system integrity for a wide range of water, gas, and industrial applications.
What is Pipe Fusion Welding?
Pipe fusion welding is a technique used to join sections of polyethylene (PE) pipe and fittings. Instead of using mechanical joints, the process uses heat and pressure to melt the pipe surfaces. The melted materials are then forced together, allowing them to mix and fuse at a molecular level as they cool. The result is a single, continuous pipeline that is as strong, or even stronger, than the original pipe itself. This homogenous joint is completely leak-proof and highly resistant to end-load pressure.
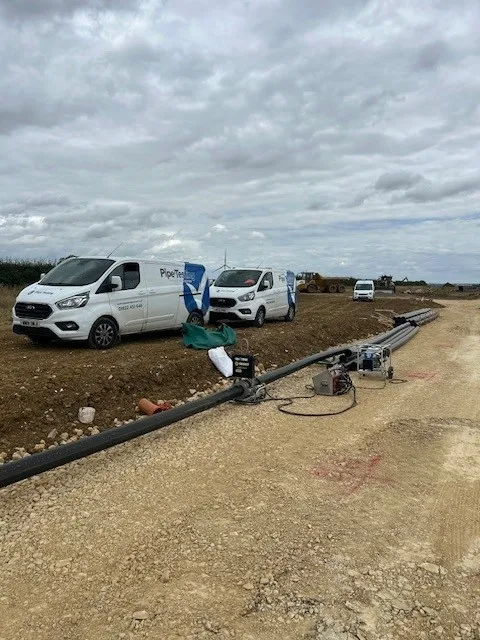
Our Pipe Fusion Welding Techniques
We offer two distinct methods of pipe fusion welding, selected based on the specific application, pipe size, and site conditions.
Electrofusion Welding
Electrofusion is a versatile method often used for repairs, connecting fittings like saddles and sockets, or for welding in challenging site conditions where a butt fusion machine may not be practical. This technique uses special PE fittings with embedded heating coils. The process involves:
- Preparation: The pipe surface is scraped to remove any oxidation and cleaned. The electrofusion fitting is then positioned over the joint.
- Welding: An electrofusion control unit is connected to the fitting. It sends a precise electrical current through the embedded coils for a calculated time.
- Fusion: The heat from the coils melts the inside of the fitting and the outside of the pipe. The materials fuse together as they expand in the confined space.
- Cooling: The joint cools and solidifies, creating a strong, reliable connection.
Discover more about our specialised Electrofusion Welding Services.
Butt Fusion Welding
Butt fusion is an ideal method for joining long, straight runs of new PE pipe of the same diameter. The process involves:
- Preparation: The ends of the two pipes to be joined are faced to create clean, parallel surfaces.
- Heating: A thermostatically controlled heater plate is inserted between the pipe ends, heating them to a specific melting temperature.
- Fusion: The heater plate is removed, and the two molten pipe ends are pressed together under controlled pressure for a set time.
- Cooling: The joint is left to cool under pressure, forming a permanent, monolithic bond.
Our skilled teams use modern butt fusion equipment to ensure every weld meets stringent quality standards. Learn more about our dedicated Butt Fusion Welding Services.
Common Applications of Pipe Fusion Welding
Our pipe fusion welding services are essential for a variety of sectors and projects that depend on the long-term integrity of PE pipelines:
- Potable Water Mains: For new installations and repairs, creating seamless and hygienic water distribution networks. After welding, new mains require Chlorination for New Construction Projects.
- Gas Distribution Networks: Providing secure, leak-free joints critical for safety in gas supply lines.
- Rising Mains & Pumping Mains: Creating durable pipelines capable of withstanding high pressures.
- Industrial Pipework: For chemical transport, wastewater, and process water systems where joint integrity is vital.
- Landfill & Geothermal Systems: For leachate collection and fluid transport lines.
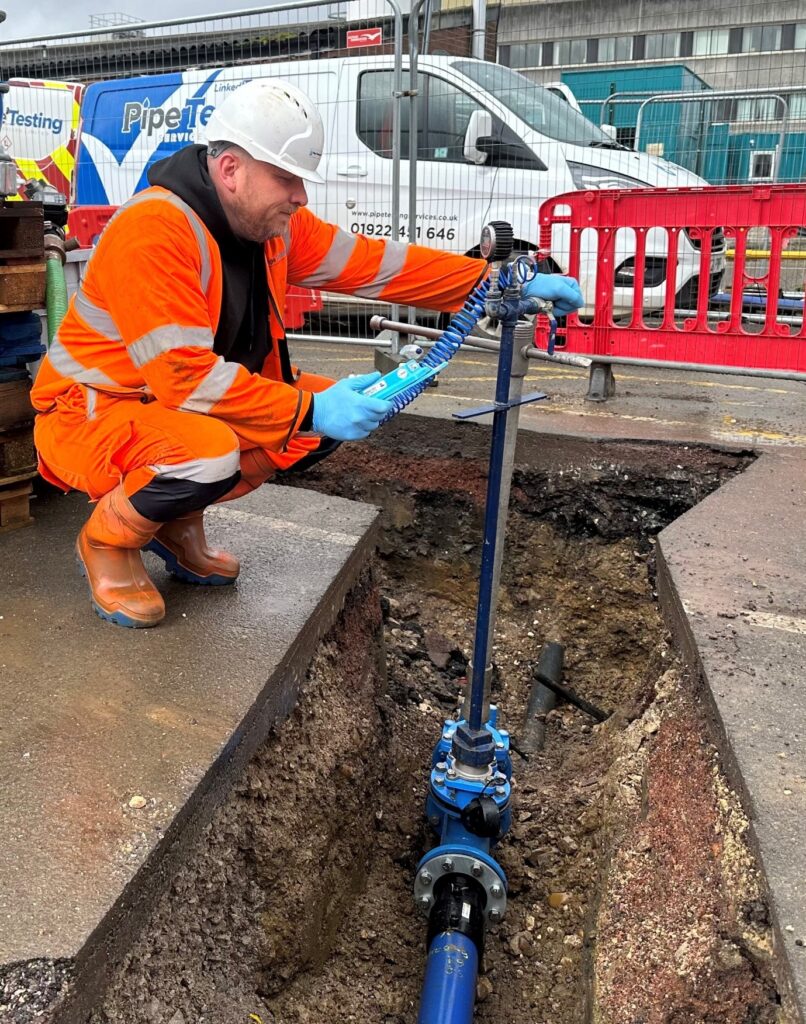
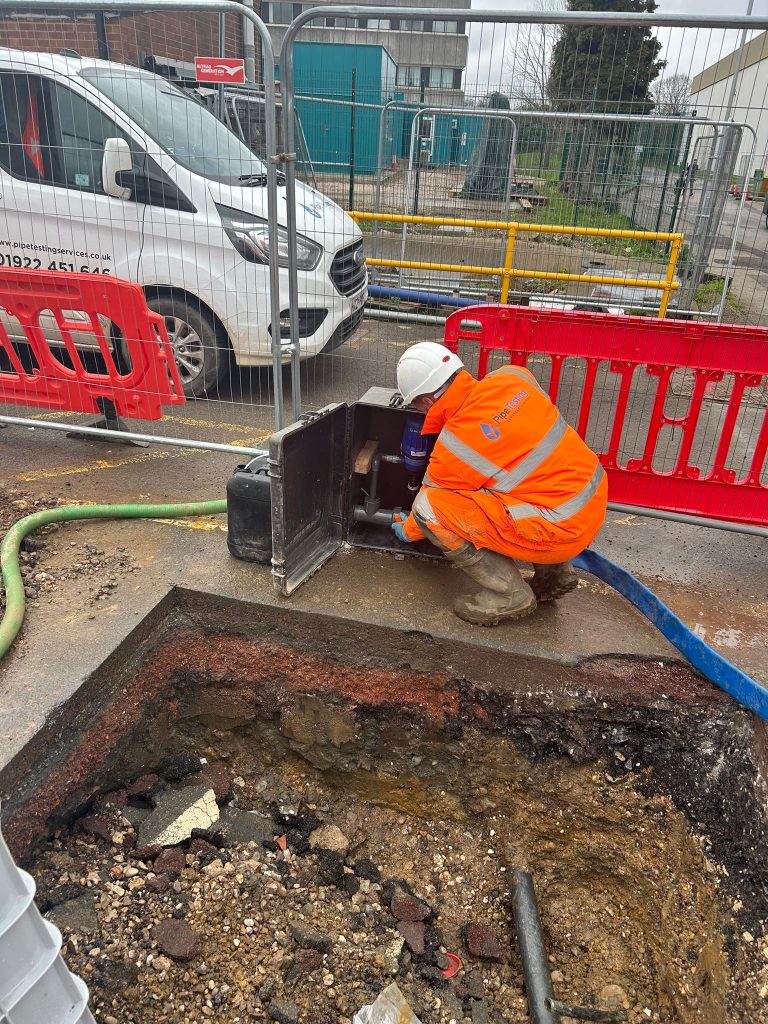
Why Choose PTS for Pipe Fusion Welding?
Certified and Experienced Technicians: Our operators are fully trained and hold EUSR qualifications, ensuring that every weld is performed to the highest industry standards.
Modern and Calibrated Equipment: We use a fleet of state-of-the-art butt fusion and electrofusion machines that are regularly calibrated and maintained to ensure precision and reliability.
Full Compliance: We adhere to all relevant UK regulations and water industry standards. Each fusion joint is logged and documented, providing a full quality assurance record for your project.
Comprehensive Project Support: Pipe fusion is often part of a larger project. We provide a complete service, including hydrostatic pressure testing to verify joint integrity and full commissioning services.
Quality Assurance and Data Logging
We, at Pipe Testing Services, prioritise quality assurance and traceability in every fusion welding project. Our teams leverage cutting-edge data logging technology to capture and record critical parameters such as heat-soak times, fusion pressures, and cooling times.
With their extensive knowledge and expertise, our fusion welding teams ensure every project is executed flawlessly, adhering to the highest industry standards.
Fusion Welding for Trenchless Pipe Installations
Trenchless pipe installation techniques have revolutionised the construction and maintenance of underground piping systems, minimising surface disruptions and environmental impact. At Pipe Testing Services, we leverage our fusion welding expertise to support these innovative trenchless methods, ensuring the highest quality and efficiency in underground pipe installations.
Our fusion welding services are compatible with a range of trenchless techniques, including:
- Horizontal Directional Drilling (HDD)
- Pipe Bursting
- Pipe Ramming
- Slip-lining
Leveraging our fusion welding expertise, we create continuous, leak-proof pipe strings by fusing high-density polyethylene (HDPE) or polyethylene (PE) pipes through butt fusion or electrofusion welding. Consequently, these pipe strings facilitate efficient installation via trenchless methods, eliminating the need for extensive excavation. This approach, in turn, reduces costs, minimises surface disturbances, and enhances overall project sustainability.
Our fusion welding capabilities allow us to fabricate custom pipe configurations, including bends, branches, and fittings. As a result, we ensure seamless integration with existing infrastructure or project-specific requirements.
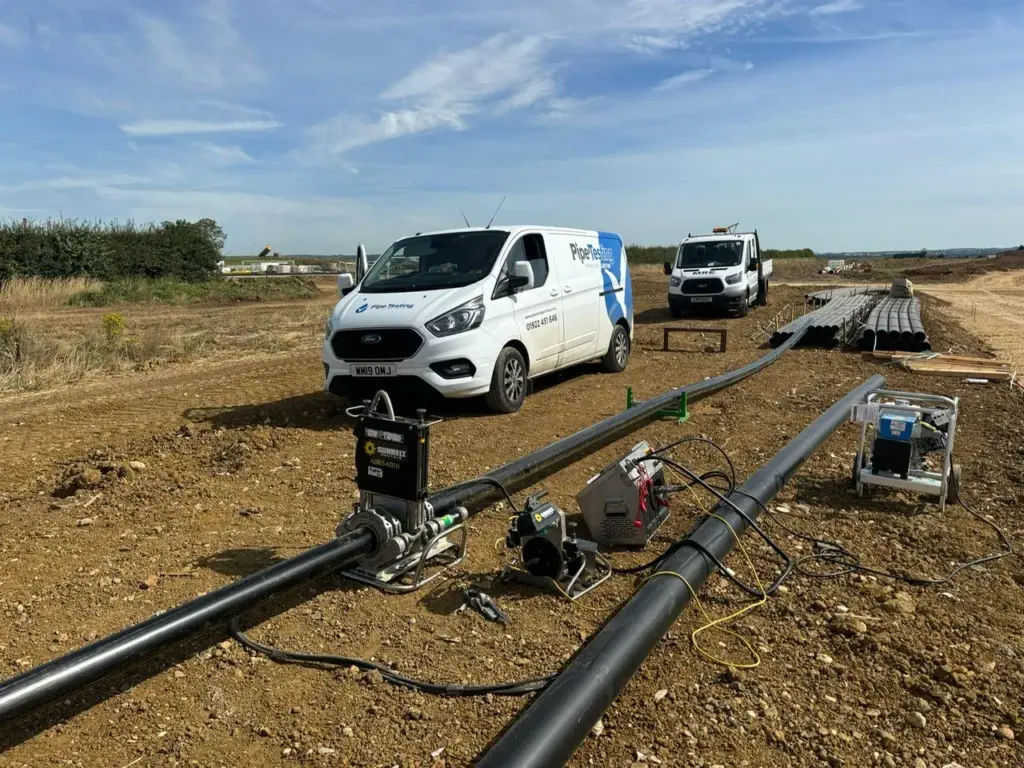
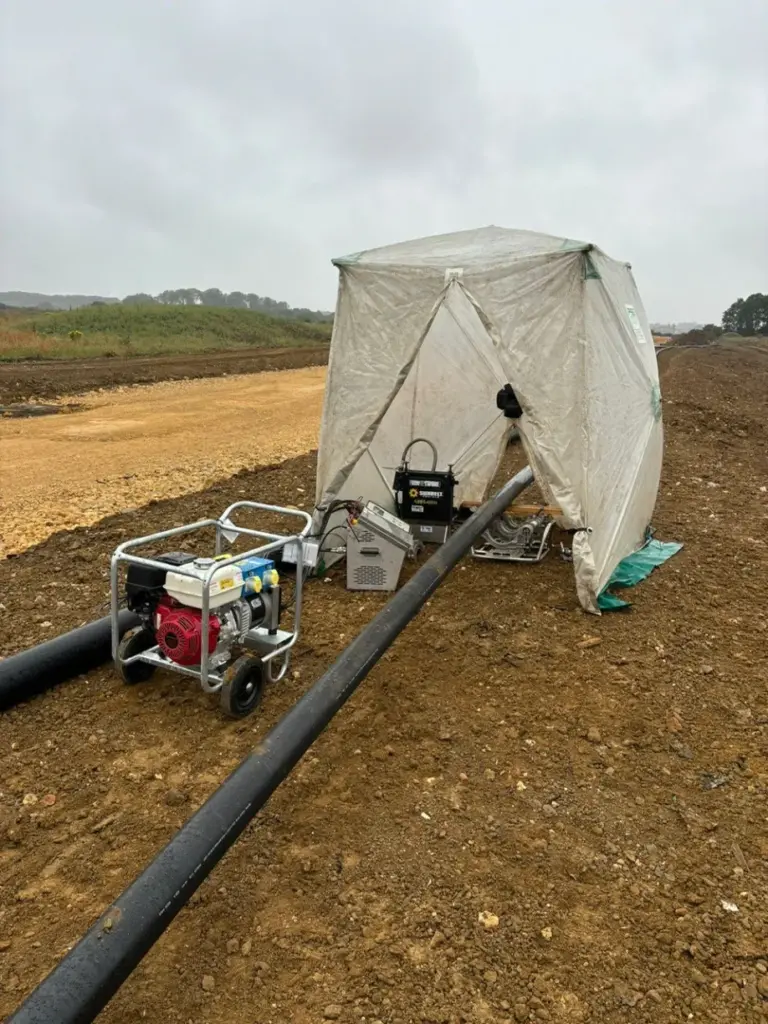
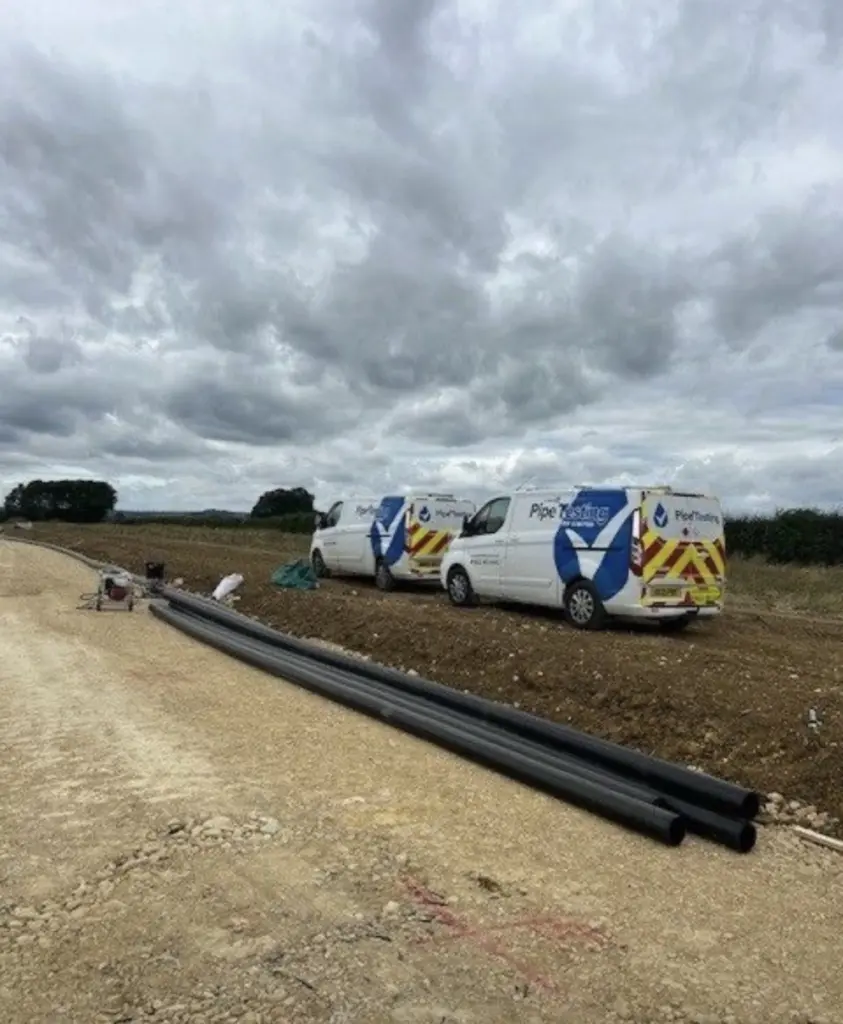
Expert Pipe Fusion Welding Services for PE Pipe Systems
Project Focus: Large-Scale Butt Fusion for New Rising Main in Leicester
Our project in Leicester involved the installation of over 1.6km of new PE rising mains for a new client. Using state-of-the-art butt fusion welding, our team expertly joined sections of 180mm and 125mm PE pipe, creating strong, continuous, and completely leak-free joints. This project highlights our capability in managing large-scale new pipeline installations from the outset. Read the full Leicester rising main case study here.
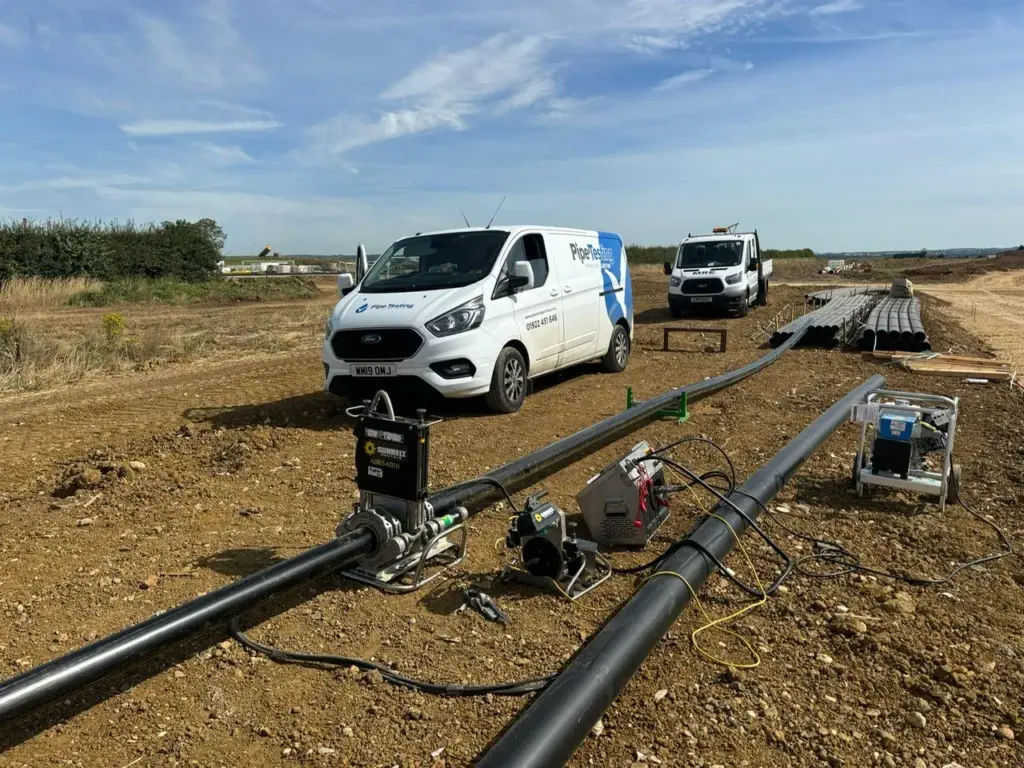
Project Focus: Electrofusion Welding for a Critical Pumping Station Connection
For a long-standing client, we were tasked with installing a new rising main and connecting it to a pumping station where a secure, leak-proof joint was essential. Our skilled engineers used specialised electrofusion welding techniques to join the HDPE pipes, creating a robust, monolithic joint stronger than the pipe itself. This ensured the long-term integrity of this critical water infrastructure. Explore the full electrofusion case study here.
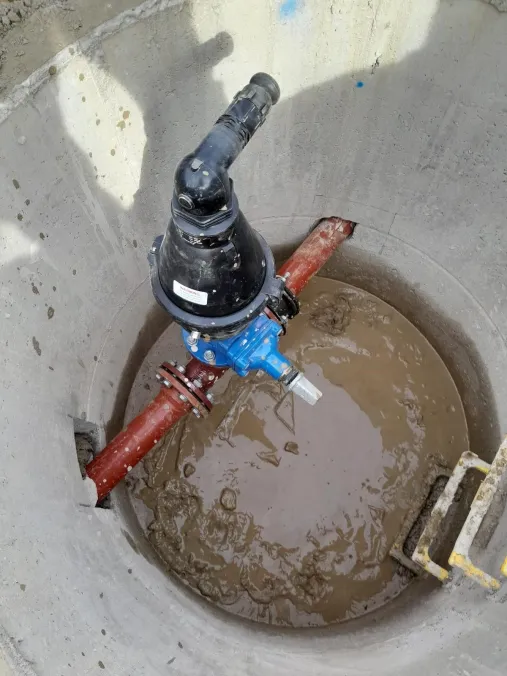
Contact Us for Your Pipe Fusion Welding Needs
For reliable, compliant, and expertly executed pipe fusion welding services, get in touch with the team at Pipe Testing Services. We provide tailored solutions for projects of all sizes across the UK.
- Phone – 01922 451646
- Email – enquiries@pipetestingservices.co.uk
- Address – Unit 27 Birchbrook Industrial Estate, Shenstone, Lichfield, Staffs, WS14 0DJ
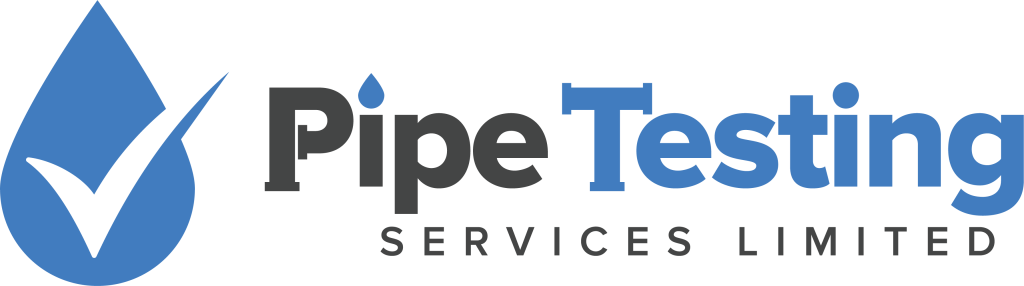

Pipe Fusion Welding FAQs
How long does a fusion welded joint take to complete?
The duration of a fusion welded joint depends on factors such as pipe diameter, ambient temperature, and the specific welding technique used. Typically, butt fusion welds can take anywhere from 15 minutes to an hour, while electrofusion welds may require 20-45 minutes.
Can fusion welded joints be repaired or modified?
Yes, fusion welded joints can be repaired or modified through electrofusion welding. This method allows for the installation of branch connections, fittings, or repair couplings without compromising the integrity of the existing pipe.
How long do fusion welded joints last?
When properly executed, fusion welded joints can last for decades, often matching or exceeding the lifespan of the pipes themselves. With regular maintenance and inspection, these joints can provide reliable service for many years.
Are fusion welded joints suitable for underground applications?
Absolutely. Fusion welded joints are extensively used in underground piping systems, such as water mains, gas distribution networks, and telecommunication infrastructure. Their leak-proof nature and durability make them ideal for buried applications.
Can fusion welding be performed in adverse weather conditions?
While fusion welding can be performed in various weather conditions, extreme temperatures or precipitation may affect the welding process. Our teams are trained to assess site conditions and take appropriate measures, such as using shelters or climate-controlled environments, to ensure optimal fusion welding results.
What pipe materials can be fusion welded?
Fusion welding is primarily used for thermoplastic pipes, with High-Density Polyethylene (HDPE) and Medium-Density Polyethylene (MDPE) being the most common materials.
What is the main advantage of a fusion weld over a mechanical joint?
A fusion weld creates a single, continuous pipe. It has no seals or gaskets that can degrade over time, making it a permanent, leak-proof solution that is highly resistant to root intrusion and ground movement.
What sizes of pipe can PTS weld?
We are equipped to handle a wide range of pipe diameters, typically from 20mm up to 630mm, covering most applications from small service connections to large trunk mains.