HDPE Butt-Welding: Creating Durable and Seamless Pipe Connections
At Pipe Testing Services (PTS), we take pride in offering top-tier pipe solutions for various industries. Among our comprehensive services, HDPE Butt-Welding stands out as an essential method for creating reliable, leak-proof pipelines. With its ability to form seamless joints, HDPE butt welding is a trusted solution in water distribution and high-pressure systems.
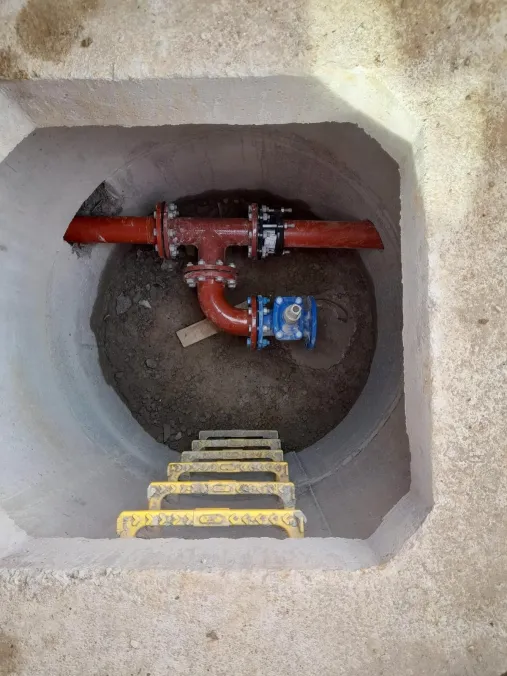
What Is HDPE Butt-Welding?
HDPE butt welding, also known as butt fusion welding, is a process of joining high-density polyethylene (HDPE) pipes by fusing their ends. Using heat and pressure, this technique creates a continuous and homogeneous pipeline with joints as strong as the original material.
Key Steps in the HDPE Butt-Welding Process
- Preparation: Pipes are cut to the required length and thoroughly cleaned. Proper preparation ensures a clean, smooth fusion.
- Facing: A facing tool shaves the pipe ends flat and parallel to optimise the welding surface.
- Heating: A heated plate (between 200°C–220°C) melts the pipe ends.
- Fusion: After removing the plate, the melted ends are pressed together under controlled pressure.
- Cooling: The joint is allowed to cool and solidify, forming a strong, durable bond.
This method ensures that pipelines remain robust, leak-proof, and capable of handling extreme pressure conditions.
Applications of HDPE Butt-Welding in Water Mains and Distribution Systems
HDPE butt-welding
plays a critical role in the water industry, providing an effective solution for building robust and long-lasting pipelines. Its reliability and efficiency make it the method of choice for:
Water Mains Installation
HDPE butt-welding ensures leak-free connections in water main installations, where maintaining consistent pressure and preventing water loss is essential. The seamless joints eliminate weak points, reducing the likelihood of failures that can disrupt water supply.
Potable Water Distribution Systems
Safety is paramount when transporting potable water. HDPE’s corrosion resistance and chemical inertness, combined with butt-welding’s ability to create smooth, continuous joints, ensure the integrity and purity of drinking water as it moves through the system.
Irrigation Networks
In agricultural and horticultural sectors, HDPE butt-welding is used to construct irrigation networks that are highly durable and capable of withstanding varying pressure conditions. The welded joints handle frequent pressure changes while preventing water loss due to leaks.
Sewer and Drainage Systems
Although primarily designed for clean water transport, HDPE butt-welding is also used in sewer and drainage applications within water distribution networks. Its corrosion-resistant properties make it ideal for carrying wastewater without the risk of pipe degradation.
Emergency Repairs and Extensions
Water distribution systems often require quick and reliable repairs to minimise service disruptions. HDPE butt-welding provides an efficient method to join pipes in emergency situations, ensuring the system resumes operation without compromising quality.
Why HDPE Butt-Welding Is Ideal for Water Systems
Corrosion Resistance
Water distribution pipelines are constantly exposed to moisture and varying environmental conditions. HDPE materials, paired with butt-welding, offer exceptional resistance to rust and chemical degradation, ensuring long-term reliability.
Leak-Free Design
For water mains and distribution systems, leakage is a major concern, contributing to water wastage and increased operational costs. HDPE butt-welded joints are seamless, eliminating the risk of leaks associated with mechanical fittings.
Strength Under Pressure
Municipal water mains and distribution systems must handle high pressures. HDPE butt-welded pipes maintain their strength and integrity, even under heavy load conditions.
Cost Efficiency in Maintenance
The durability of HDPE butt-welded pipelines reduces maintenance costs and downtime, a crucial factor in managing large-scale water distribution networks.
Adaptability
HDPE butt-welding supports a range of pipe sizes, from small bore pipes for residential areas to large-diameter mains supplying towns and cities.
Environmental Sustainability
HDPE is a recyclable material, and its long service life reduces the need for frequent replacements. This aligns with sustainable practices in modern water management.
Challenges of HDPE Butt-Welding and How PTS Overcomes Them
While HDPE butt-welding is highly effective, success depends on expertise and equipment. Challenges include:
- Alignment and Cleanliness - Misaligned or contaminated pipes can compromise joint integrity.
- Environmental Conditions - Weather conditions, such as wind or temperature fluctuations, may affect weld quality.
- Operator Skill - Proper technique is vital for achieving reliable welds.
At PTS, we address these challenges by employing:
- Certified Technicians: Our team undergoes extensive training in HDPE butt welding.
- Advanced Equipment: We utilise state-of-the-art machines for precise temperature and pressure control.
- Rigorous Quality Assurance: We implement visual inspections, phased array ultrasonic testing (PAUT), and other advanced methods to ensure every joint meets or exceeds standards.
HDPE Butt-Welding vs. Electrofusion Welding
Both HDPE butt-welding and electrofusion welding are popular for HDPE pipe connections. While butt welding creates a seamless bond, electrofusion welding uses couplers with built-in heating elements to join pipe ends.
Key Differences:
Feature | HDPE Butt-Welding | Electrofusion Welding |
Joint Type | Seamless, homogeneous bond | Mechanical joint |
Cost | Lower for large-scale projects | Higher due to fittings |
Ease of Use | Requires skilled operators | More user-friendly |
Pipe Diameter Range | Wider (63mm to 900mm) | Limited by coupler sizes |
Why Choose Pipe Testing Services for HDPE Butt-Welding?
As an industry leader, PTS delivers expert HDPE butt-welding services tailored to your project. Our approach includes:
- Comprehensive Solutions – From preparation to quality assurance, we handle every aspect of the welding process.
- Tailored Services – We adapt welding parameters to suit your pipe dimensions and project requirements.
- Compliance Assurance – Our work adheres to all relevant standards, ensuring safety and reliability.
- Nationwide Coverage – With teams across the UK, we bring our expertise to you.
Other Pipework Services from PTS
In addition to HDPE butt-welding, PTS provides:
- Legionella Risk Assessments
Ensure compliance and water safety with our comprehensive surveys.t - Chlorination Services
Maintain pipeline hygiene with our disinfection solutions. - Electrofusion Welding
Ideal for smaller pipe diameters or where additional fittings are required. - Hydrostatic Pressure Testing
Verify the strength and integrity of pipelines under pressure. - Flow Surveys and Water Tank Commissioning
Ensure efficient water management and storage solutions.
These services complement HDPE butt-welding, providing comprehensive solutions for your pipeline and water system needs.
Quality Assurance for HDPE Butt-Welding at PTS
Our commitment to quality sets us apart. Each HDPE butt-welding project undergoes:
- Visual Inspections: Assessment of weld bead uniformity and consistency.
- Non-Destructive Testing (NDT): Advanced methods like phased array ultrasonic testing (PAUT) verify joint integrity.
- Destructive Testing: Sample joints are subjected to tensile and bend tests to validate strength.
By maintaining strict quality control, we deliver reliable results that stand the test of time.
Contact Pipe Testing Services
At PTS, we combine expertise, advanced equipment, and exceptional service to meet your HDPE butt-welding needs. Whether you’re managing a large-scale pipeline project or maintaining existing infrastructure, we’re here to help.
Contact us today to discuss your requirements, request a quote, or learn more about our services.
- Phone: 01922 451646
- Email: enquiries@pipetestingservices.co.uk
- Address: Unit 27 Birchbrook Industrial Estate, Shenstone, Lichfield, Staffs, WS14 0DJ
Trust Pipe Testing Services for unparalleled quality, precision, and reliability.
FAQs About HDPE Butt-Welding
What is HDPE butt-welding used for?
HDPE butt-welding is commonly used to join HDPE pipes in water mains, gas pipelines, industrial fluid transport, and chemical processing systems.
How does HDPE butt-welding differ from electrofusion welding?
HDPE butt-welding creates a seamless joint without additional fittings, while electrofusion welding uses couplers with built-in heating elements for the connection.
What pipe sizes can be joined using HDPE butt-welding?
HDPE butt-welding is suitable for pipes ranging from 63mm to 900mm in diameter, making it versatile for various projects.
What are the advantages of HDPE butt-welding in high-pressure systems?
It provides leak-free, corrosion-resistant joints capable of withstanding high pressures, ensuring durability and reliability in demanding environments.
Can HDPE butt-welding be performed in cold or windy conditions?
Environmental factors like temperature and wind can affect weld quality, but skilled technicians and proper equipment, like those used by PTS, mitigate these challenges.
How do you ensure the quality of HDPE butt-welded joints?
At PTS, we perform visual inspections, non-destructive testing (PAUT), and destructive testing on sample joints to guarantee weld integrity.
Is HDPE butt-welding cost-effective?
While initial equipment costs may be higher, the seamless joints reduce maintenance and replacement costs, making it cost-effective in the long run.
Why should I choose Pipe Testing Services for HDPE butt-welding?
PTS offers certified technicians, advanced equipment, and nationwide service, ensuring high-quality welding tailored to your needs.