Butt-Welding: An Essential Technique in Pipe Testing Services
At Pipe Testing Services (PTS), we pride ourselves on offering a wide range of high-quality services, ensuring the integrity and safety of your piping systems. One of the core techniques we specialise in is butt-welding.
This technique, integral to pipe testing and maintenance, offers unmatched strength, reliability, and efficiency in joining pipes. Whether you’re dealing with water systems, chemical processing, or oil and gas pipelines, the technique provides a secure and durable solution.
In this blog, we’ll delve deep this type of welding, its benefits, applications, and how it integrates with our other key services like hydrostatic pressure testing, pipe fusion welding, and chlorination.
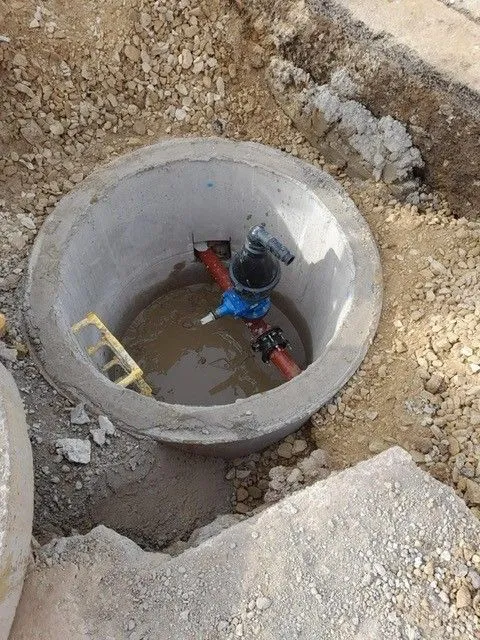
What is Butt-Welding?
Butt-welding is a technique used to join two pipes or fittings by aligning their ends and applying heat and pressure until they fuse together. This method ensures a full penetration weld, resulting in joints that are as strong as the parent material. It is commonly used in the construction and maintenance of pipelines where durability and safety are paramount.
At Pipe Testing Services, we utilise butt fusion welding to ensure each joint is optimally bonded, preventing leaks and enhancing the overall performance of your pipeline.
Key Advantages of Butt-Welding
Strength and Durability
The joints created are as strong as the parent material. The process of heat fusion ensures a strong molecular bond that is resistant to pressure, corrosion, and environmental wear.
Cost-Effective
Compared to other pipe joining techniques, butt-welding is highly economical. It requires minimal reinforcement and fasteners, and the joint can be made directly at the site without the need for expensive materials or equipment.
Versatility
It is compatible with a wide range of materials, including HDPE butt welding, carbon steel, and stainless steel, making it suitable for various industries and applications.
Minimal Material Waste
Unlike some other methods, butt-welding requires less filler material, which reduces waste and lowers overall project costs.
Efficiency
The technique can be automated or manually performed, providing flexibility to suit the needs of different projects. Whether it’s for small-scale pipework or large infrastructure projects, this technique can be adapted accordingly.
Applications of Butt-Welding Across Industries
- Water Infrastructure
In water systems, butt-welding is commonly used for polyethylene pipe fusion in water distribution and waste management systems. It creates strong, leak-proof joints that are resistant to pressure fluctuations, ensuring the reliable flow of water. - Oil and Gas
The oil and gas industry relies heavily its ability to handle high-pressure environments. Thermoplastic pipe welding is essential in creating secure connections for pipelines that transport oil and gas across vast distances. - Chemical Processing
In chemical plants, where durability and chemical resistance are crucial, this technique ensures that pipes can withstand harsh chemicals without risk of leaks or degradation.
Technological Advancements in Butt-Welding
Recent innovations in butt fusion welding equipment have improved the precision, speed, and quality of the welding process. Modern automated systems can make precise, full-penetration welds with minimal human intervention, enhancing both efficiency and safety.
Additionally, advanced fusion bonding techniques have been developed to cater to newer materials and larger diameter pipes, further expanding the versatility of butt-welding.
Comparing Butt-Welding with Other Welding Methods
When it comes to pipe joining, there are several methods to choose from, including electrofusion and butt-welding. Let’s take a look at how these methods compare:
Butt-welding
This technique requires the pipe ends to be aligned and fused together using heat and pressure. This method is ideal for high-pressure systems and is widely used in water, gas, and chemical pipelines.
Electrofusion welding
This technique on the other hand, uses a fusion coil to generate heat that melts the pipe ends. It’s often used in tight spaces where butt-welding equipment might not be feasible. While electrofusion is versatile, it is generally better suited for smaller diameter pipes and lower-pressure systems.
At Pipe Testing Services, we offer both techniques to provide the best solution for your project, whether you need the high-strength joints of butt-welding or the flexibility of electrofusion.
Find out more here – Pipe Fusion vs. Traditional Pipe Joining: Which is Better for Preventing Leaks?
Butt-Welding and Sustainability
One of the standout benefits of butt-welding is its contribution to sustainable practices in pipeline construction and maintenance. By providing strong, leak-resistant joints, this type of welding helps to prevent water and chemical leakage, reducing the environmental impact of pipeline systems. Additionally, the minimal use of filler material during the welding process helps reduce waste, making it an eco-friendly choice.
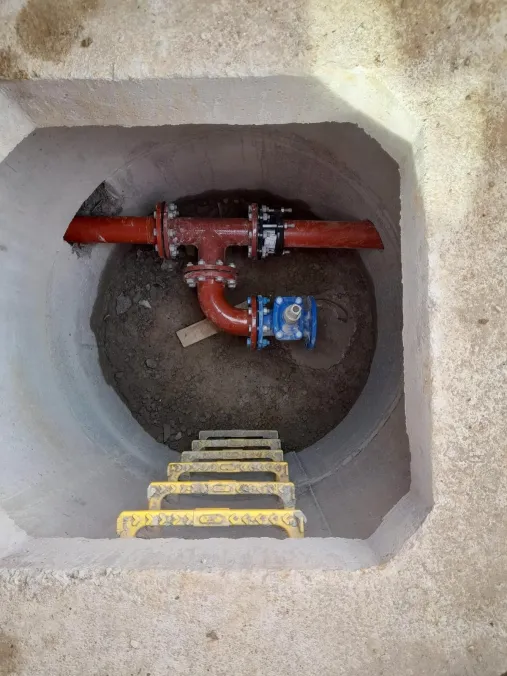
Challenges in Butt-Welding and How We Overcome Them
While butt-welding is a highly reliable technique, it is not without its challenges. Some common issues include:
- Pipe Alignment: Proper alignment is critical to ensure a high-quality weld. At Pipe Testing Services, we use state-of-the-art equipment to guarantee precise alignment before the welding process.
- Material Compatibility: Different materials require different welding techniques. We carefully assess the materials involved to ensure the correct welding process is used for optimal results.
- Heat Management: Too much heat can result in weak welds, while too little can lead to incomplete fusion. Our skilled technicians monitor and control heat levels to ensure perfect results every time.
Training and Certification for Butt-Welding Operators
Proper training and certification are essential for ensuring high-quality butt-welding. At Pipe Testing Services, our operators undergo rigorous training in both manual and automated welding techniques. We adhere to the highest industry standards to ensure our welds meet the necessary regulatory requirements.
Contact Pipe Testing Services
For exceptional butt-welding and expansive, expert fusion fusion welding, and other related services, please reach out to Pipe Testing Services using the following contact information:
- Phone: 01922 451646
- Email: enquiries@pipetestingservices.co.uk
- Address: Unit 27 Birchbrook Industrial Estate, Shenstone, Lichfield, Staffs, WS14 0DJ
We are committed to delivering reliable and reputable services to ensure the safety and compliance of your pipeline systems. Contact us today to discuss your needs and receive a personalised quotation that ensures the highest quality of service.
Don’t wait for leaks or structural failures. Schedule your butt-welding service today and ensure the long-lasting integrity of your piping systems.