Specialist Socket Fusion and Saddle Fusion Welding Services
Pipe Testing Services (PTS) provides expert socket fusion and saddle fusion welding services across the UK. These specialised techniques are essential for creating strong, reliable, and leak-proof connections for polyethylene (PE) pipes, particularly for joining smaller diameter pipes and creating branch connections on existing mains. Our certified technicians have the expertise to deliver precise results for a range of applications.
Understanding Socket Fusion Welding
Socket fusion is a technique used to join smaller diameter PE pipes (typically up to 125mm) with socket fittings, such as couplings and elbows. This method creates a permanent, monolithic bond ideal for residential and commercial water supply lines.
The Socket Fusion Process
- Preparation: The pipe end and the inside of the socket fitting are thoroughly cleaned and prepared.
- Heating: A specialised heating tool with male and female ends is used. The outside of the pipe end and the inside of the socket fitting are heated simultaneously to a molten state.
- Fusion: The tool is removed, and the molten pipe end is immediately pushed into the molten socket fitting.
- Cooling: The joint is held under pressure for a short period while it cools and solidifies, creating a joint that is as strong as the parent pipe.
Applications for Socket Fusion
- Joining smaller diameter PE pipes in water distribution networks.
- Industrial applications requiring small-bore, corrosion-resistant pipework.
- Creating durable connections for residential and commercial plumbing systems.
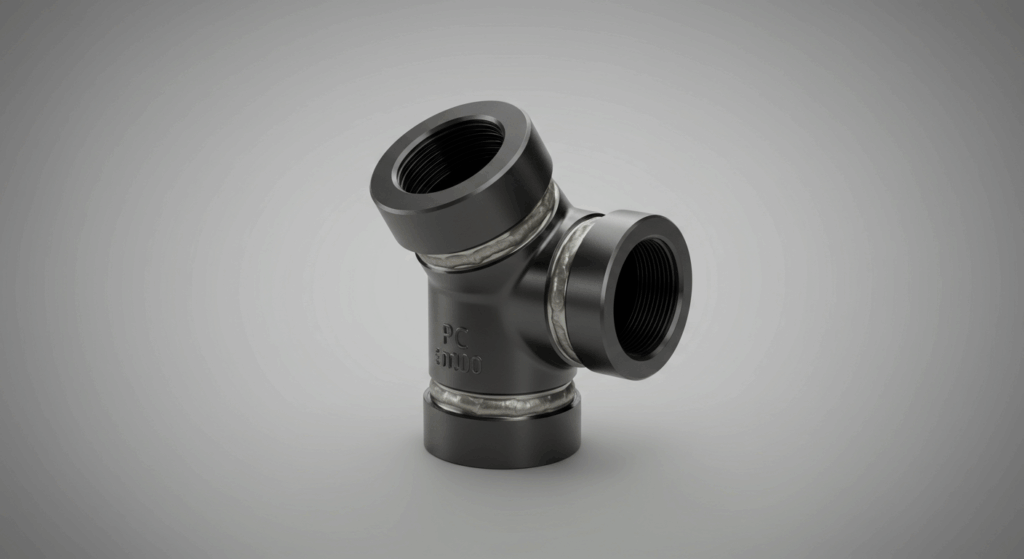
Understanding Saddle Fusion Welding
Saddle fusion is an indispensable technique used to add a branch connection to the side of an existing, larger PE main. This is often done to install a new service line without cutting the main pipe, making it a highly efficient process.
The Saddle Fusion Process
- Preparation: The surface of the main pipe where the saddle will be attached is cleaned and scraped to remove any surface oxidation. The base of the saddle fitting is also prepared.
- Heating: A concave heater is used to heat the surface of the main pipe, while a convex heater simultaneously heats the base of the saddle fitting.
- Fusion: The heaters are removed, and the saddle fitting is immediately placed onto the heated area of the main pipe under controlled pressure.
- Cooling: The joint cools and solidifies, creating a strong, leak-proof branch connection. The pipe can then be tapped (drilled) through the new fitting if required.
Applications for Saddle Fusion
- Creating new service connections on municipal water and gas distribution systems.
- Adding outlets, branches, or sensor points to existing industrial pipelines.
- Maintaining the structural integrity of the main pipeline while expanding the network.
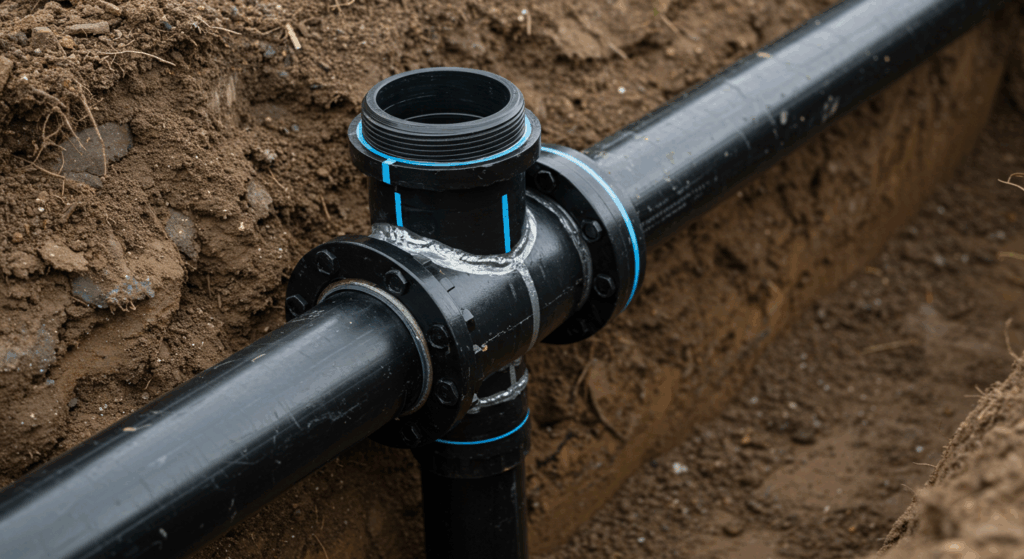
Quality Assurance and Professional Execution
The success of any fusion weld depends on the quality of the workmanship. At Pipe Testing Services, we place a strong emphasis on quality assurance for every socket and saddle fusion project. Our technicians undergo rigorous training and follow industry best practices to ensure consistent, reliable results. As a key part of our overarching Pipe Fusion Welding Services, we ensure every joint is made to the highest standard.
Choose PTS for Unparalleled Socket and Saddle Fusion Services
When it comes to ensuring the long-term integrity of your PE pipe systems, trust the experts at Pipe Testing Services. Our skilled teams have the expertise to deliver flawless, leak-free socket and saddle fusion welded joints.
Contact us today to learn more about our specialised fusion welding services or to request a quote for your upcoming project.
- Phone – 01922 451646
- Email – enquiries@pipetestingservices.co.uk
- Address – Unit 27 Birchbrook Industrial Estate, Shenstone, Lichfield, Staffs, WS14 0DJ
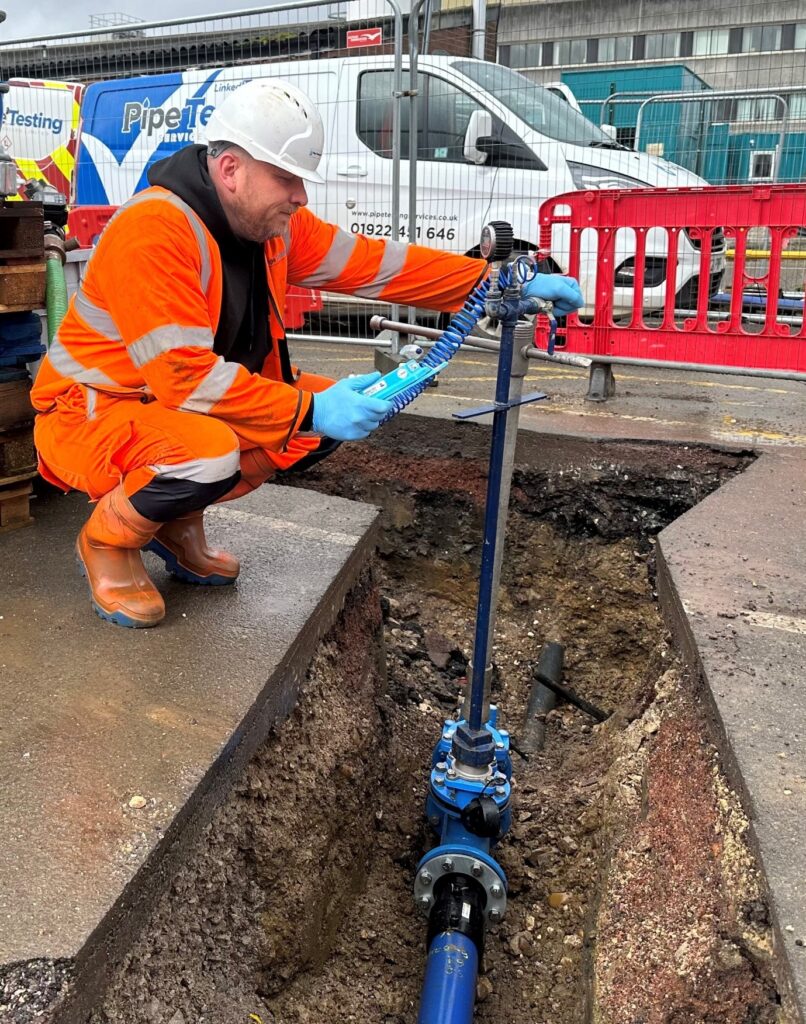
Saddle Fusion & Socket Fusion - (FAQs)
What are the main advantages of socket and saddle fusion?
Socket and saddle fusion create leak-proof, monolithic joints that are virtually as strong as the parent pipe material. They require no filler materials and result in a homogeneous connection. These fusion joints are also resistant to vibration, pull-out forces, and temperature fluctuations.
What pipe materials can be fusion welded?
Fusion techniques like socket and saddle fusion are ideal for thermoplastic pipes like polyethylene (PE), polypropylene (PP), and polyvinyl chloride (PVC). However, they cannot be used on non-thermoplastic pipe materials.
How long does it take to complete a socket or saddle fusion weld?
The actual fusion welding time is relatively quick once the components are heated, usually just a few minutes. However, the overall process including preparation, heating, cooling, and inspection can take 30 minutes to a couple of hours depending on the pipe size.
Are there any size limitations for socket and saddle fusion?
Socket fusion is generally limited to PE pipes up to 12 or 16 inches in diameter. Saddle fusion can accommodate larger diameter pipes up to around 48 inches, making it ideal for municipal water mains.
How are socket and saddle fusion welds inspected and tested?
Completed welds are visually inspected for uniformity and defects. Non-destructive testing methods like guided side bend tests can check for fusion quality. Destructive tests like joint restraint or tensile tests may also be performed.
Can socket or saddle fusion joints be repaired if issues arise?
No, socket and saddle fusion joints cannot be repaired or re-worked once the cooling phase is complete and the plastic is re-solidified. If defects are found, the joint must be completely cut out and re-done.
How does pipe diameter affect saddle fusion?
Saddle fusion becomes more critical for larger diameter pipes because the branch outlet area increases significantly. Proper saddle fusion prevents leaks and ensures the integrity of the entire pipeline system.